address:201, Factory 6, Longhui Industrial Park, Fuqiao 3rd District, Xinhe Community, Fuhai Street, Baoan District, Shenzhen china
What are the key factors that should be considered in PCB layout?
Designing compact and efficient printed circuit boards (PCBs) is at the heart of the modern electronics industry, and with the rise of the Internet of Things and smart factories, production machinery contains more and more electronics, and meeting these expectations is the job of the PCB design. As PCB mount components become more compact, designers face new challenges. To help you, KFPCBA has highlighted 5 dos and don'ts that will help you avoid potential problems that may arise.
1. Choose the correct solder mask gap
We need to use a solder mask to protect our PCBs from corrosion and contamination. In theory, we should use solder mask on all areas where we don't want solder to be placed. In practice, this means preventing solder mask from spreading where it is not needed.
Solder mask is a sticky material that continues to spread after application. If the solder mask is allowed to contaminate the pads, it will prevent proper solder joints from being formed. Therefore, the design should have a small gap between the outer edge of the pad and the solder mask. This is called the solder mask gap. This gap may vary depending on how the mask is applied and is best determined after discussion with the PCB manufacturer.
2. Consider the fine pitch connector
Solder Mask Width Solder mask width becomes critical when we consider the space between the pads of components such as connectors. The distance between component terminals is called the pitch. As electronic components get smaller, so do the distances between their terminals. It is common to find connectors with a pitch of 1.00mm and below (as well as other smaller pitch components), which creates additional challenges for us as PCB designers.
When securing a fine pitch connector to a PCB, the distance between the pads needs to be carefully considered. We already mentioned that we need a gap between the edge of the pad and the solder mask. If the two component pads are close enough, leaving a gap on both sides may not provide enough surface area for the solder mask to properly adhere to the PCB between those pads. In these cases, thin strips of solder mask can lift and contaminate the solder joints, affecting solder wetting and creating bad solder joints that may go undetectable.
Therefore, it is important to discuss this with our PCB manufacturer when designing pads for fine pitch connectors. They may also raise this as an issue on any PCB when they have completed a Design for Manufacture (DFM) review. Manufacturers can advise on how to proceed, which may include removing solder mask between pads.
3. Consider through-hole solutions
The advent of surface mount technology (SMT) is one of the greatest innovations in PCB design. Surface mount components make manufacturing faster and easier to automate, increasing factory throughput and capacity. However, surface mount may not be the correct solution for some applications.
Choosing through-hole terminations may seem like a step backwards, but sometimes physical advantages make them ideal. Copper pads for SMT components can be small and fastened on a small area PCB. Electronic devices are stressed during their lifetime, whether by vibration, shock or tension, requiring additional mechanical strength. In this case, the terminals through the PCB will provide robustness and stability that SMT technology cannot.
4. Don't forget the connectors
It's important that we don't get so focused on the pads that we forget to make room for the connector. The placement of the connector on the PCB is critical to allow space for the connector body to avoid conflict with other components. This is especially important for modern compact designs where board space is at a premium.
There are additional requirements when using right-angle connectors. Connectors designed to be fastened to the edge of a PCB are typically used in backplane or panel mount applications, and their placement is critical for proper spacing on the board itself. When putting them into our designs, we had to make sure to pay close attention to the dimensions announced by the manufacturer.
Data sheets and PCB schematics will provide this data, but using CAD models will save time and prevent errors. We should always check the manufacturer's website to make sure we are using the latest information.
5. Optimize your mass production
Design The design phase is over and our product is ready for release. Our concept has been proven and our task is to turn the design into a production-ready device. Designs optimized for testing and prototyping may not be suitable for mass production.
When our device is released to the market, we need to determine if the design features (such as test points) that are required during testing are really needed. Using cheaper high-volume manufacturing techniques may not preserve the design tolerances used on the prototype PCB. Working with a production PCB manufacturer is critical as the design approaches production. This will help avoid delays and ensure our PCBs are designed for high volume manufacturing and its associated cost-effectiveness.
Understanding and planning are key
The small size of modern electronic components makes PCB design challenging. However, understanding potential pitfalls and planning our designs accordingly can prevent problems before they occur. By following the rules of PCB design and choosing a partner who can provide all the necessary information, it is possible to create elegant and compact designs that will serve customers for many years.
-
No comment
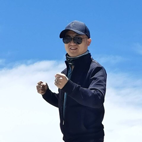